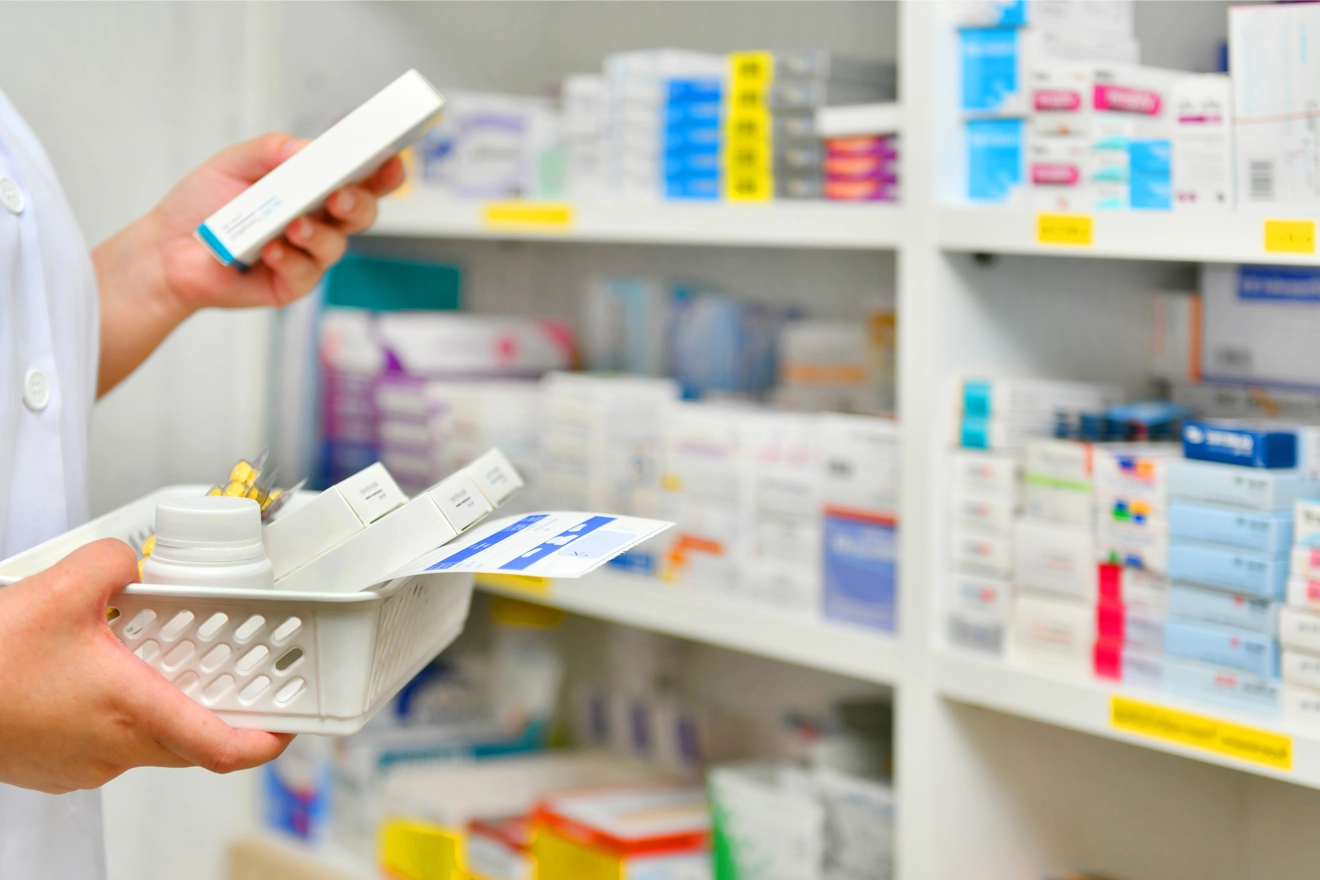
A pharmaceutical label is a monologue between the drug manufacturer and the patients. Miscommunication of any kind can affect the end-user. To protect the interest of the patient population, global Health Authorities (HAs) closely monitor pharmaceutical labels and indications of pre-approval. There are various components to a label and with each additional component, the chances of errors increase gradually.
It takes approximately ten (10) to fifteen (15) years for a pharmaceutical company to develop and market a promising new drug. Errors in pharmaceutical labeling frequently occur due to wrong reference information, inconsistencies in the labeling process, competency gaps, and much more. Preventing labeling errors is as crucial as preventing inaccuracies in the drug development process. Mishaps with country-specific labeling can cost pharmaceutical companies thousands of dollars in wasted inventory.
Over the years, HAs have identified key areas where a company can rethink its ‘pharmaceutical label’. Enlisted below are few points to be considered
Nonconformity to Labeling Regulations
A pharmaceutical company’s marketing activities get compromised because of dynamic regulations resulting in compliance issues. A few significant labeling compliance issues are:
- Delays in submission of updated safety information on the drug label such as a Summary of Product Characteristics (SmPC), Patient Information Leaflet (PIL), etc.
- Labeling disparity such as warnings mentioned in Core Data Sheets (CDS), is absent in local labels.
An error in labeling, results in incompliance and more effort and cost to the drug manufacturers as they have to validate their entire labeling process again to mitigate the error.
Solution: A Standard Operating Procedure (SOP) adoption, in addition to a lean governance structure, helps foresee all regulation requirements on the organizational level as and when required.
Drug manufacturers can ease the compliance pressure by having a modernized and developed labeling system. Such a solution can help companies adhere to the GxP guidelines across the labeling process. Experts in the domain can help drug manufacturers respond to unexpected Regulatory changes, which makes it easier to track and trace labeling developments.
Labeling Readability Error
Mandatory statements that carry crucial information printed inappropriately can cause readability issues for many consumers and could be a significant source of medication errors. Some of the readability issues are:
- Embossed or clear labels lacking contrast to help read the text
- Size/fonts, label clutter, and poor legibility of labels
- The non-linear barcode on the blister strip which is non-scannable
Solution: Here’s what drug manufacturers can do to enhance the readability of their product labels:
- A proper barcode to provide vital information on the product like expiry dates, batch numbers/lot numbers, unique serial numbers, etc.
- Color-coded labels to emphasize critical information
- A significant contrast between the background and font color
- Recommended suitable spacing of at least 3mm between lines
Incorrect Labeling Information
Drug manufacturers ensure that labeling information is precise for medical professionals and consumers for understanding a drug. Any information discrepancy can lead to medication errors resulting in higher medication costs or even patient death. A few medication errors due to misprinted information are:
- Ambiguous dosage indication lacking space between dose/strength and unit of measure
- Look-alike medication because of shared linguistic properties between two (02) or more names
- Poor labeling on the blister strip because of inadequate medical information
- Wrong usage of symbols on the labels such as abbreviations
Solution: To minimize the risk of printing wrong information, drug manufacturers can voluntarily use in-house expertise or source it from experts in the domain. These sources provide insights on associated risks of drug labels and hence offer remediation of labeling services in the post-marketing approval process.
Country-specific Labeling Errors
Often, drug manufacturers launch their drug products in different countries having different labeling requirements. A language error in a country-specific label can delay the product launch. Adhering to the local authority labeling guidelines requires professional expertise in translation to minimize the risk of error.
Solution: To gain better insights into local labeling errors, drug manufacturers must follow and update their labeling procedures and be compliant with the specific regional authorities. It maintains the flow of the supply chain process and avoids unnecessary delays.
So, What’s Next?
Incorporating the latest technologies in labeling provides better ways to mitigate potential risks by facilitating speed and flexibility in the labeling process. Companies must keep the below-enlisted points in mind to avoid any errors leading to delays in approvals:
- A holistic and systemic approach
- Improved and integrated automated technology
- Global labeling compliance
- Overcome obstacles - Monitor, measure, report, and repeat
Negligence in labeling can cost drug manufacturers an enormous amount. Having a well-integrated system in place aids pharmaceutical companies in adapting to dynamic Regulatory labeling requirements. To avoid labeling errors and delay in approvals from Regulatory Authorities, reliance on a quality check right from the first step is paramount. Freyr, as a Regulatory labeling professional, is well-versed with the industry and can provide compliant labeling solutions. Contact us for end-to-end labeling solutions.